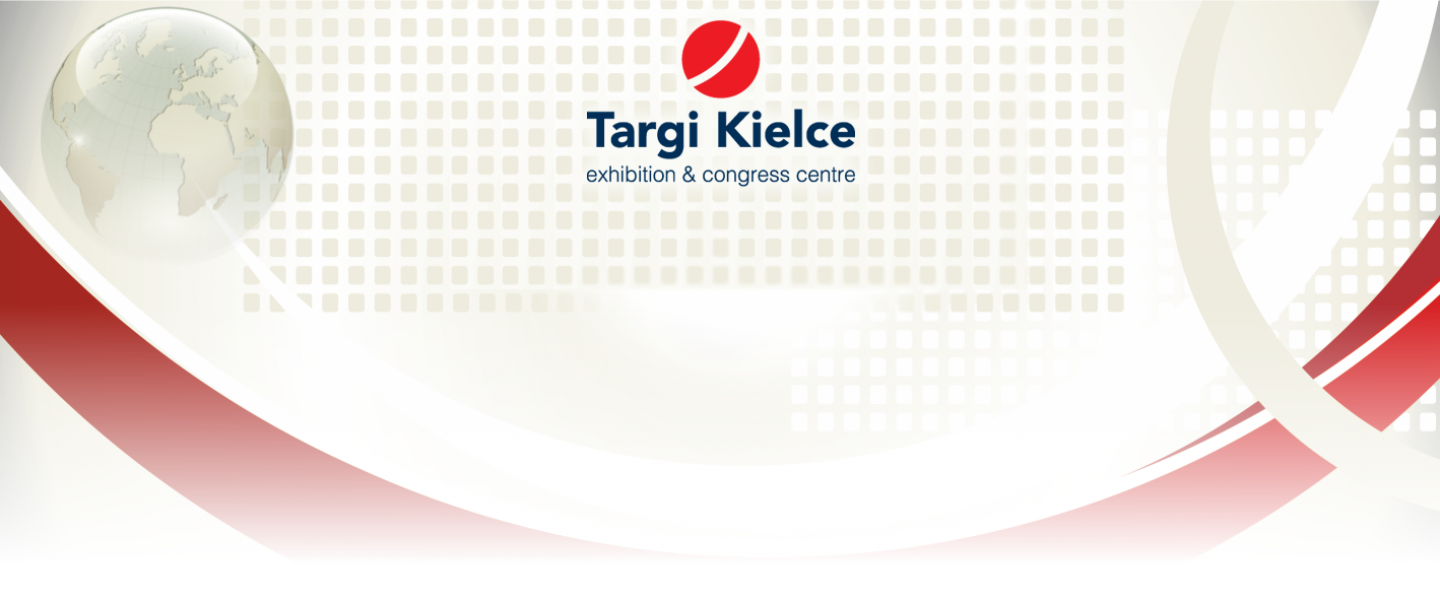
10.05.2019
The F-3 expo stand is the showcase for the Austrian brand which presents 3 work cells. One of the cells - a fully automatic system for moulding cartridges change over when the process requires just a minute
The second live presentation of Engel - production of ready-to-sell lids made in one shot technique proves that IML concepts can be economical even in short series. The company will also present a unique, compact servo hydraulic injection moulding machine able to combine maximum efficiency, performance and precision even in multi-component processes which utilise elastomers and thermoplastics.
- Poland is now the growth leader in Europe - says Piotr Nachilo, President of ENGEL Polska - Last year, according to the Central Statistical Office (GUS) data, the GDP index increased by 5.1 percent. Poland’s experiencing the market-up trend boom top. The Central and Eastern Europe’s prosperity has continued for two years. The domestic market’s good situation triggers into excellent moods before the upcoming trade fair.
Fully automated production change over system showcased at Plastpol
By concentrating on the small size of the party, Engel becomes a part of an important trend presented during Kielce’s PLASTPOL 2019 expo. In many areas, the number increases when it comes to different products on offer, thus the production sector has to deal with even smaller batches. Examples - consumer goods, such as stationery, technical details from the automotive and electro technical industries. There is also a range of products for medical technology. Economical production of various details by injection moulding is often based on the use of moulds with exchangeable cartridges. The Engel solution has been developed together with Braunform (Bahlingen, Germany) and other strategic partners. The machine exhibited at this year's trade fair show that this trend goes one step further. The presented system enables fully automatic mould inserts change over in just a minute. The injection moulding machine - Engel emotion 170/120 TL has been equipped with the Braunform patented quick changeover mechanism.
To show this new solution potential, two elements of caliper of different geometry each are produced one after the other. This is done with the quick changeover function. After just ten operations, the injection moulding machine sends the signal to the integrated articulated Engel Easix robot that the batch has been completed and unlocks the cartridges in the mould. The robot first removes the last detail produced and then changes the gripper and exchanges mould inserts. This process takes only a minute without defective details. The communication between the injection moulding machine and the periphery is handled by production management system delivered by the Engel - TIG subsidiary.
The different masses of injected details are among the biggest challenges associated with this application. In spite the fact that after the changeover, a good detail was created, the injection moulding machine constantly optimizes the settings based on three intelligent assist systems from the inject 4.0 Engel software. The iQ weight control adjusts the injection volume for each injection, iQ clamp control selects the optimum clamping force and automatically sets the force. iQ flow control performs automatic temperature differences adjustment in the medium thermostat on the basis of measured values acquired from the eflomo. Then adjusts the pump power in the thermostatic systems in order to respond to the current process conditions.
The Plastpol expo is the chance to feature a very compact design of the work cell. This will certainly attract particular attention. The centrally located easix robot is responsible for all mould inserts and details manipulations, marking of parts and assembly, and for calipers delivery. The injection moulding machine, the gripper station and the mould inserts, a laser printer, a mounting installation and a transport system are placed star-shape around the robot. The arrangement ergonomics of individual elements is positively influenced by the tie bar-less closing unit of the e-motion TL injection moulding machine. Unrestricted access to the mould area allows the robot to move freely, very close to the closing unit.
Production of ready-to-sell lids in the one shot technique - live presentation in Kielce
On-line production of ready-to-sell lids made in one shot technique proves that IML concepts can be economical even in short series. Engel thus combines the e-motion 740/220 injection moulding machine equipped with a linear viper 20 with IML uni-LINE from the Gdynia-based TMA AUTOMATION. The viper robot retrieves a label from the IML slot, places it in the form of an injection moulding machine, whilst removing the last made detail and re-transmits it to the uni-LINE for release. Thanks to the standardized installation concept, the integration of the compact IML socket is very simple. In a short time, the injection moulding machine can be flexibly converted to perform other tasks - with In-Mold-Labelling or without IML. Thus IML becomes an attractive option when designing processes also outside the high-speed segment.
TMA AUTOMATION specialises in the IML and downstream processes automation such as assembly, quality assurance and palletizing outside the high-speed area. As the ENGEL general contractor it also tackles the arrangements issues with its automation partners. Clients are provided a complete production socket from a single source. This also increases efficiency - fewer interfaces mean faster configuration.
Efficient precision in multi-component processes - the use of silicone
Competitive production of flat gaskets and O-rings - this is the strength of Engel flexseal. The International Fair of Plastics and Rubber Processing PLASTPOL showcases the extremely compact servo-hydraulic injection moulding machine. The machine proves its ability to combine maximum efficiency, effectiveness and precision even in multi-component processes with the use of elastomers and thermoplastics. The expo is the live presentations stage for the Engel flexseal 500/300 injection moulding machine with the 3000 kN clamp force. PBT inserts will injected over with hard silicone (HTV) . The quality of the two-component membranes will be controlled immediately after production with the use of the vision control system. ENGEL provides fully integrated systemic solution for this purpose. The group of partners includes the materials producer: Mesgo (Gorlago, Italy), ORP producers Stampi (Viadanica, Italy) and Giasini (Grassobbio, Italy) and Proplast Plastic Innovation Field (Rivalta Scrivia, Italy), responsible for CAD design.
The material will be fed with a rotary funnel designed and manufactured by ENGEL and equipped with a roto feeder screw. The rotating funnel with counter-rotor screw continuously transports the hard silicone without any air bubbles in. Constant pressure thus ensures a very high process safety level.
The details are transferred by the ENGEL easix articulated robot. In this case it works with the Anyfeeder manipulator from Asyril (Villaz-St-Pierre, Switzerland). The flexi-seal injection moulding machine has been specially adapted to the O-ring manufacturers and flat gaskets requirements. It can be used for all common rubber and silicone mixtures. Thanks to the horizontal machine construction and the screw injection unit the system guarantees a very high applications precision when small and medium injection weight is required. Flexiseal also enables fully automatic production with traditional brush systems.
Compiled by (KK)
Recommended news